Table of contents
In today's competitive manufacturing landscape, efficiency is paramount. Discover the advantages of integrating rebuilt CNC lathes and machine tools into your production line, and how doing so can enhance both productivity and cost-effectiveness. This exploration delves into the world of refurbished machinery, demonstrating how strategic investments can lead to substantial improvements in operational throughput.
Understanding Rebuilt CNC Machinery
In the competitive realm of manufacturing, efficiency and precision engineering play pivotal roles in a company's success. Rebuilt CNC lathes and machine tools represent a cost-effective solution for businesses aiming to enhance productivity without compromising on quality. Rebuilding, often referred to as 'retrofitting,' goes beyond mere repairs—it's a thorough overhaul that breathes new life into previously owned machinery. During this process, worn components are replaced, technology updates are installed, and adherence to current standards is ensured, resulting in a machine that operates like new. Businesses that opt for rebuilt CNC machine tools not only benefit from improved manufacturing efficiency but also contribute to sustainability by extending the equipment's life cycle. The head of manufacturing operations, with their in-depth technical expertise, can attest to how retrofitting existing equipment with advanced controls and software can yield remarkable upticks in production capabilities, pushing a facility to the forefront of innovation while keeping costs in check.
The Advantages of Rebuilt Equipment
When it comes to optimizing operational efficiency, rebuilt CNC lathes and machine tools present a plethora of advantages that extend beyond mere cost savings. Opting for refurbished CNC equipment translates to a significant reduction in expenditure when contrasted with the hefty price tags of brand-new models. In the realm of sustainable manufacturing, choosing to repurpose machinery is a testament to a company's commitment to environmental stewardship. This practice not only conserves valuable resources but also contributes to minimizing industrial waste, aiding in the global effort to reduce carbon footprints. The concept of equipment longevity is inherent in the rebuilding process, as each piece is meticulously restored to its optimal performance, often incorporating upgrades that enhance functionality. Additionally, production line integration is streamlined when introducing rebuilt tools, as they are frequently compatible with existing systems, allowing for a swift and seamless transition. It is advisable for a sustainability manager to delve into the topic of rebuilt machinery, paying particular attention to the 'life cycle assessment', a technical term that quantifies the environmental impact of a product throughout its entire existence—from creation to disposal.
Ensuring Quality and Reliability
To ensure that rebuilt CNC lathes and machine tools meet high standards of quality and reliability, it is imperative to engage with certified rebuilders who adhere to strict quality assurance protocols. Reputable rebuilders meticulously inspect and refurbish each component, aligning their practices with established reliability standards. This commitment to excellence is further reinforced by rigorous equipment certification processes, which often involve achieving ISO certification—a benchmark for quality management and operational consistency in the manufacturing industry. Additionally, machine tool accuracy is not left to chance; it is systematically verified against performance criteria to guarantee the precision that end-users demand. The quality control supervisor, a key figure in the rebuilding process, ensures that these standards are consistently met, representing an unwavering dedication to delivering dependable machinery. In this context, recognizing industry leaders such as SAMO Machine Tools is indicative of the high level of craftsmanship and reliability that professional rebuilders can offer.
Maintenance and Support for Rebuilt Machinery
Ongoing maintenance is pivotal in ensuring that rebuilt CNC lathes and machine tools operate at peak productivity and enjoy an extended machine lifespan. A well-delineated maintenance schedule forms the backbone of this process, incorporating both preventive maintenance and, as the head of maintenance would emphasize, predictive maintenance strategies. Preventive maintenance involves regular, scheduled service to prevent breakdowns, whereas predictive maintenance utilizes advanced techniques to forecast and mitigate potential issues before they arise. This proactive approach not only boosts productivity enhancement but also safeguards against unexpected downtime and costly repairs. Additionally, robust technical support plays an integral role in maintaining these complex machines, offering guidance and swift problem resolution. Users must have access to a knowledgeable support team that can provide assistance and advice to ensure the smooth operation of their rebuilt machinery.
Maximizing ROI with Rebuilt CNC Tools
Businesses looking to maximize their return on investment in the competitive world of manufacturing should consider the advantages of rebuilt CNC lathes and machine tools. With cost efficiency being a paramount concern, opting for rebuilt equipment can offer significant savings in terms of lower initial purchase prices. This strategic decision directly impacts the total cost of ownership, a critical factor that financial controllers analyze thoroughly. Beyond the acquisition cost, rebuilt CNC tools typically lead to lower downtime, as they are often restored to like-new conditions, ensuring reliable performance and less interruption in production. Investment recovery is further enhanced by the potential for customized CNC solutions that rebuilt tools provide. By tailoring equipment to specific production needs, businesses can optimize their operations, often at a fraction of the cost of brand-new machinery. The seamless integration of refurbished machinery into existing production lines can lead to a swift and substantial improvement in overall productivity and, consequently, a faster return on investment.
Similar articles
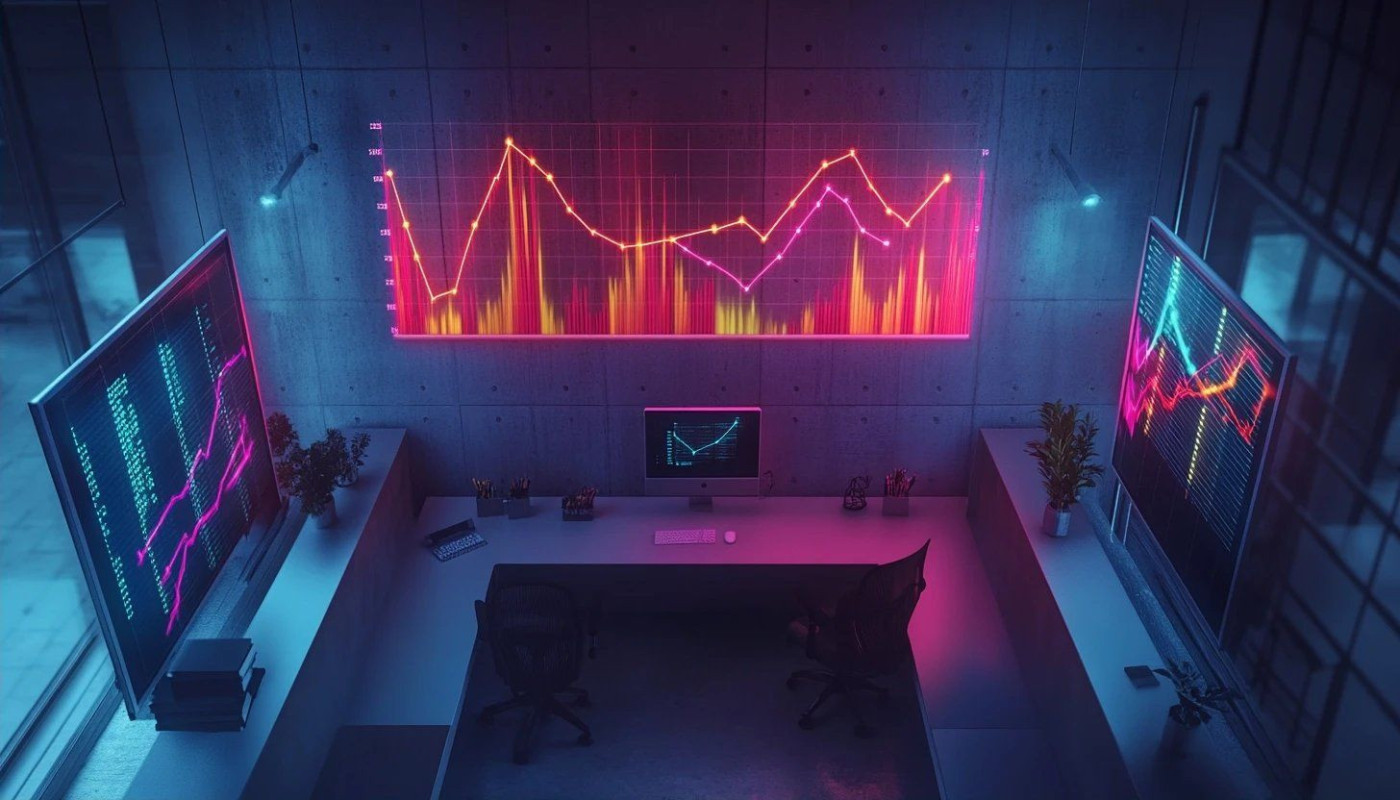
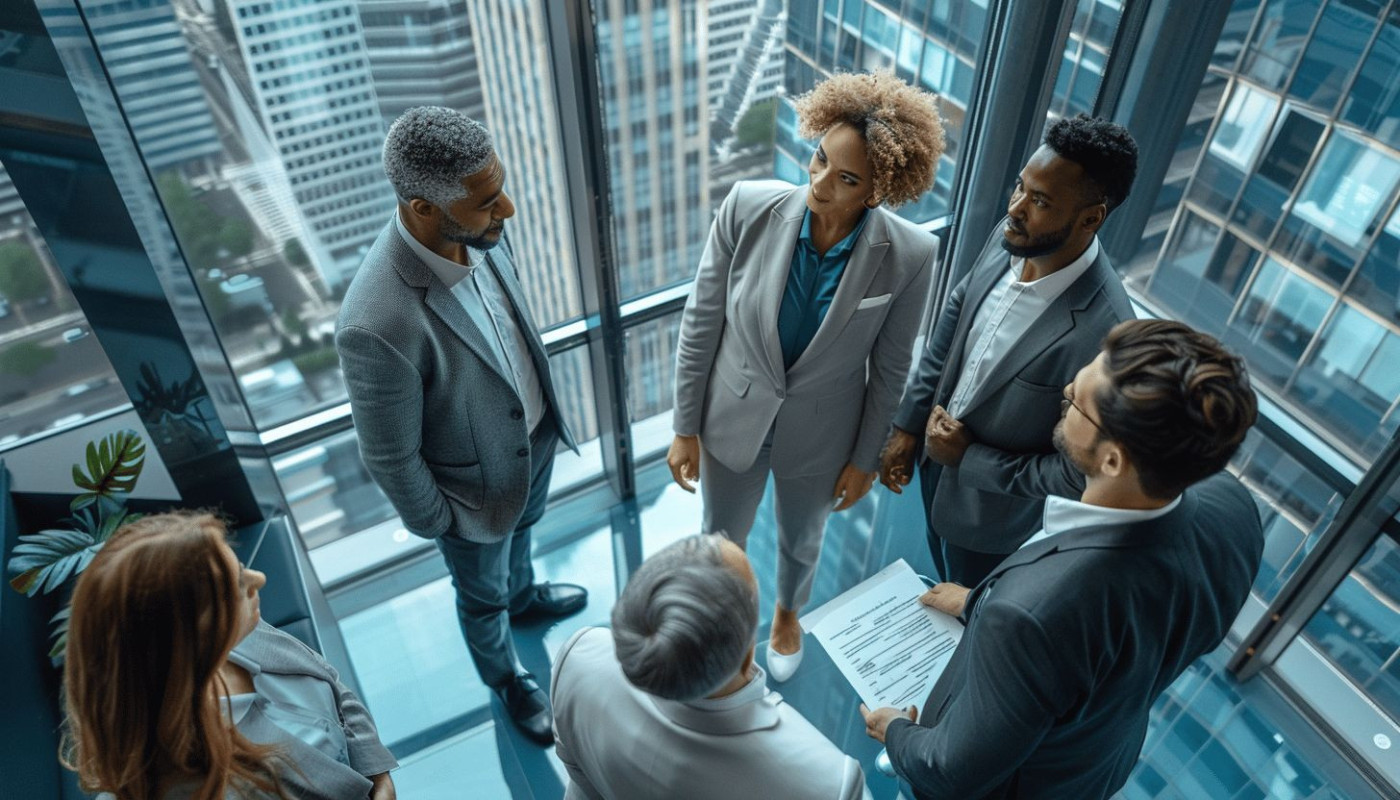
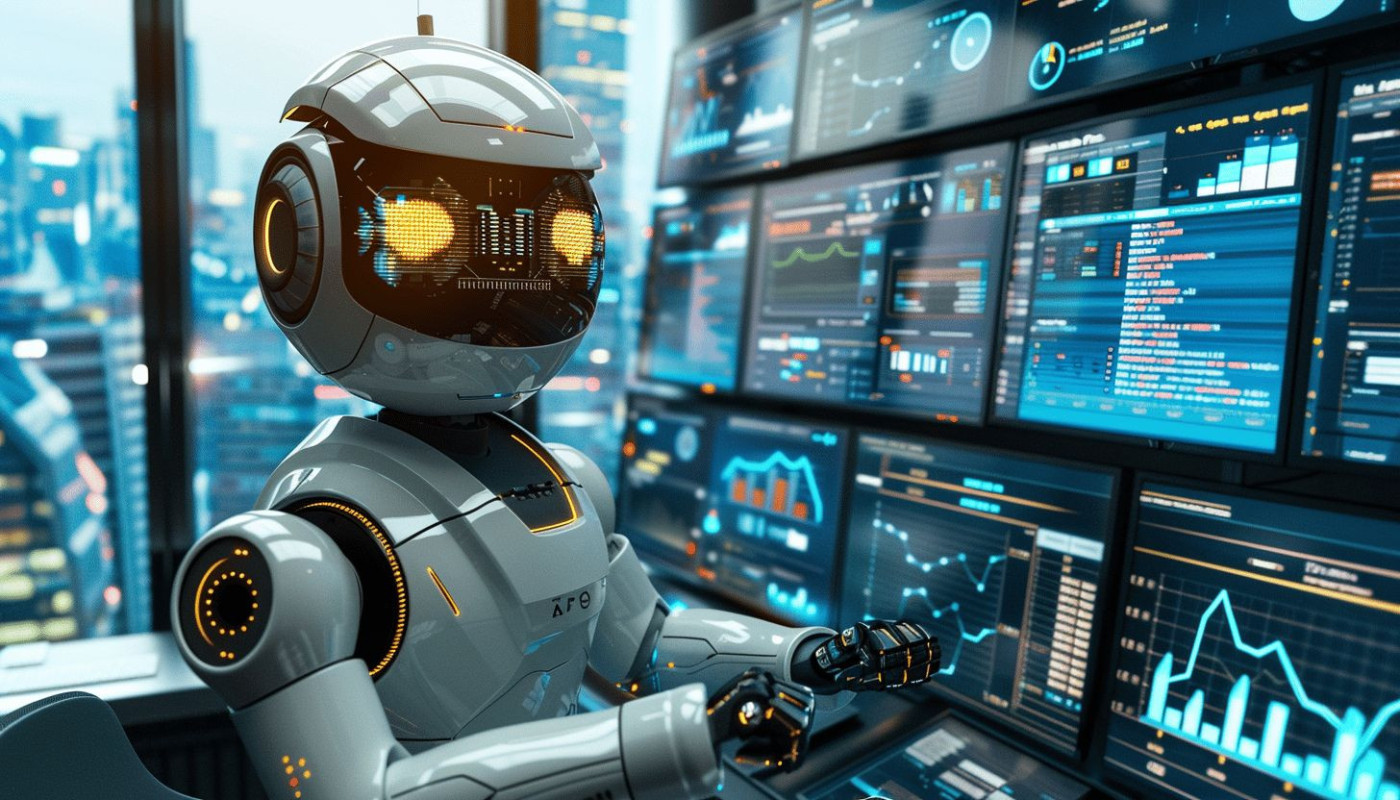
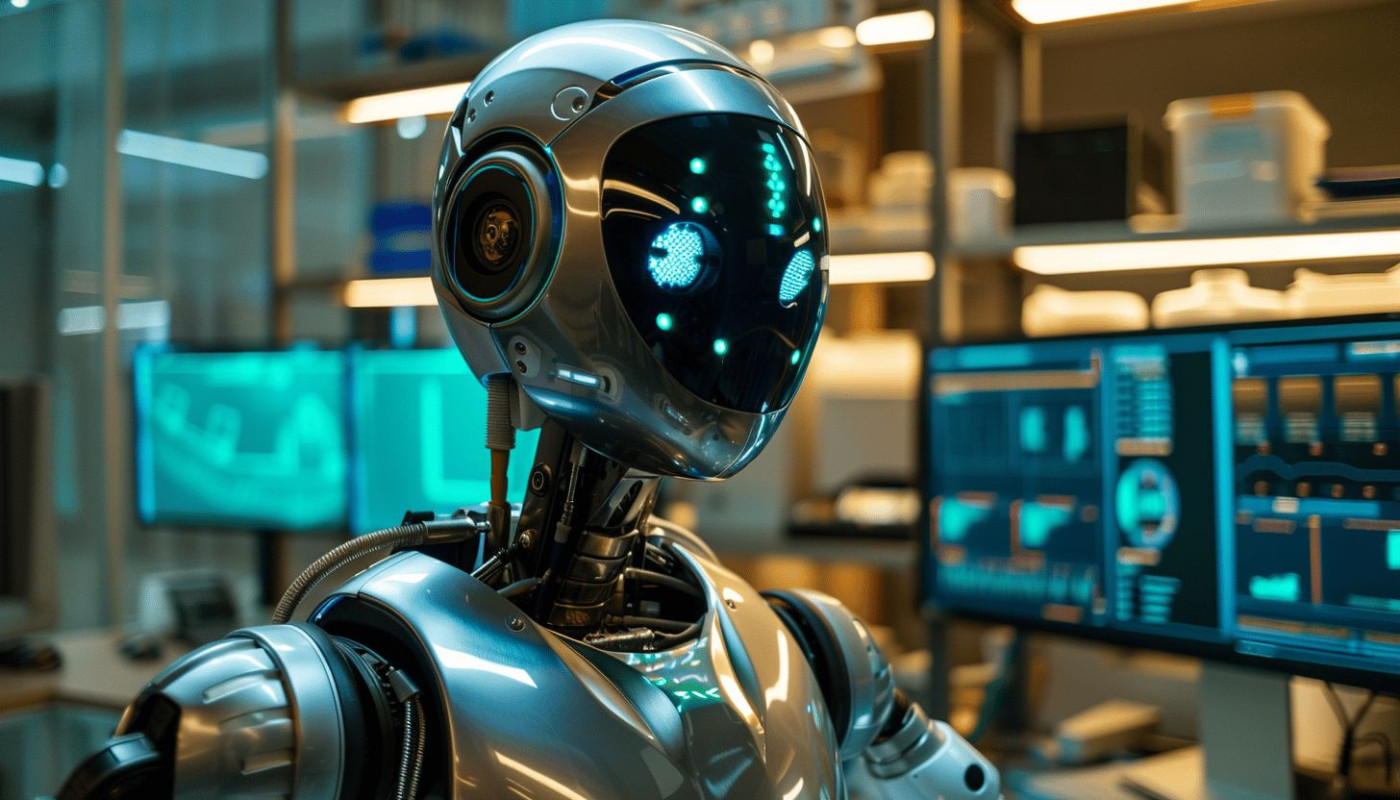
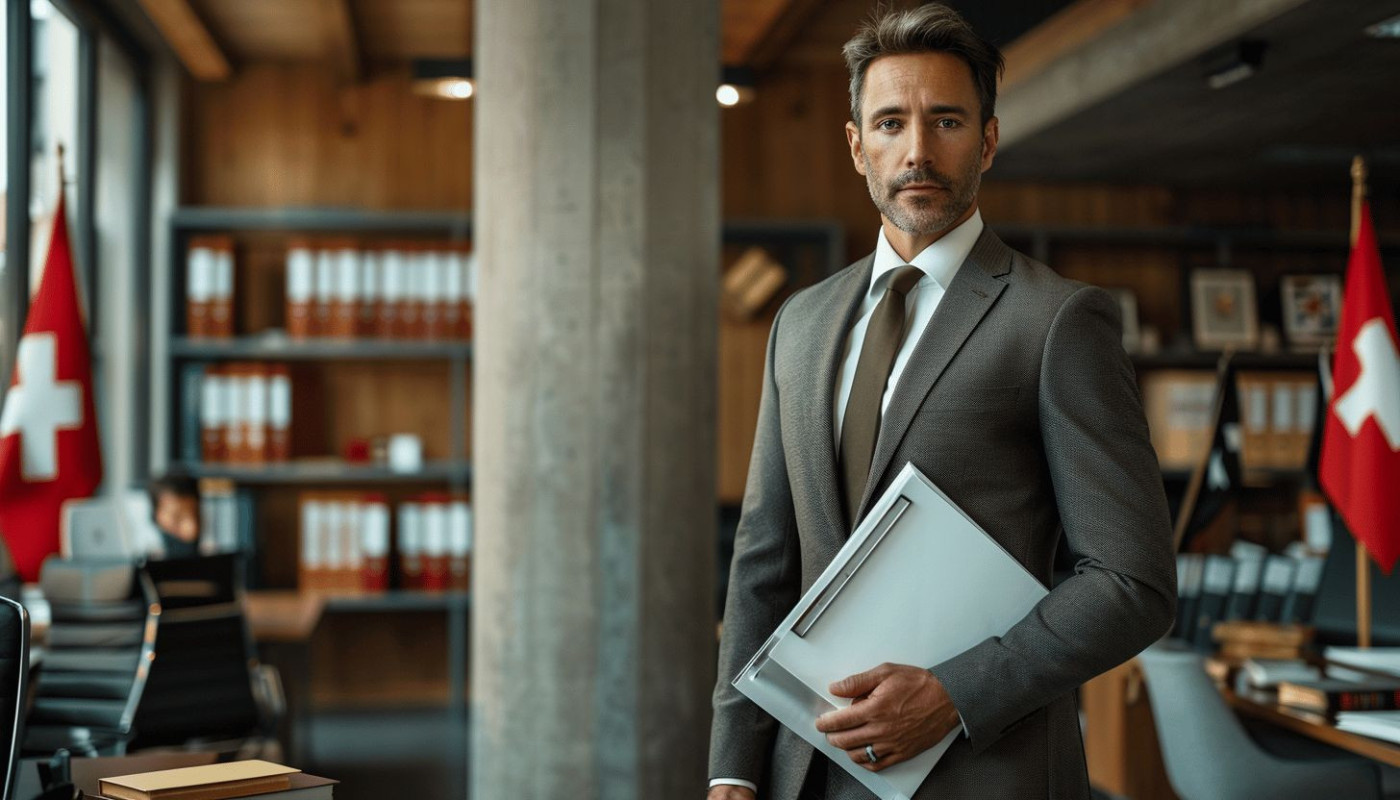

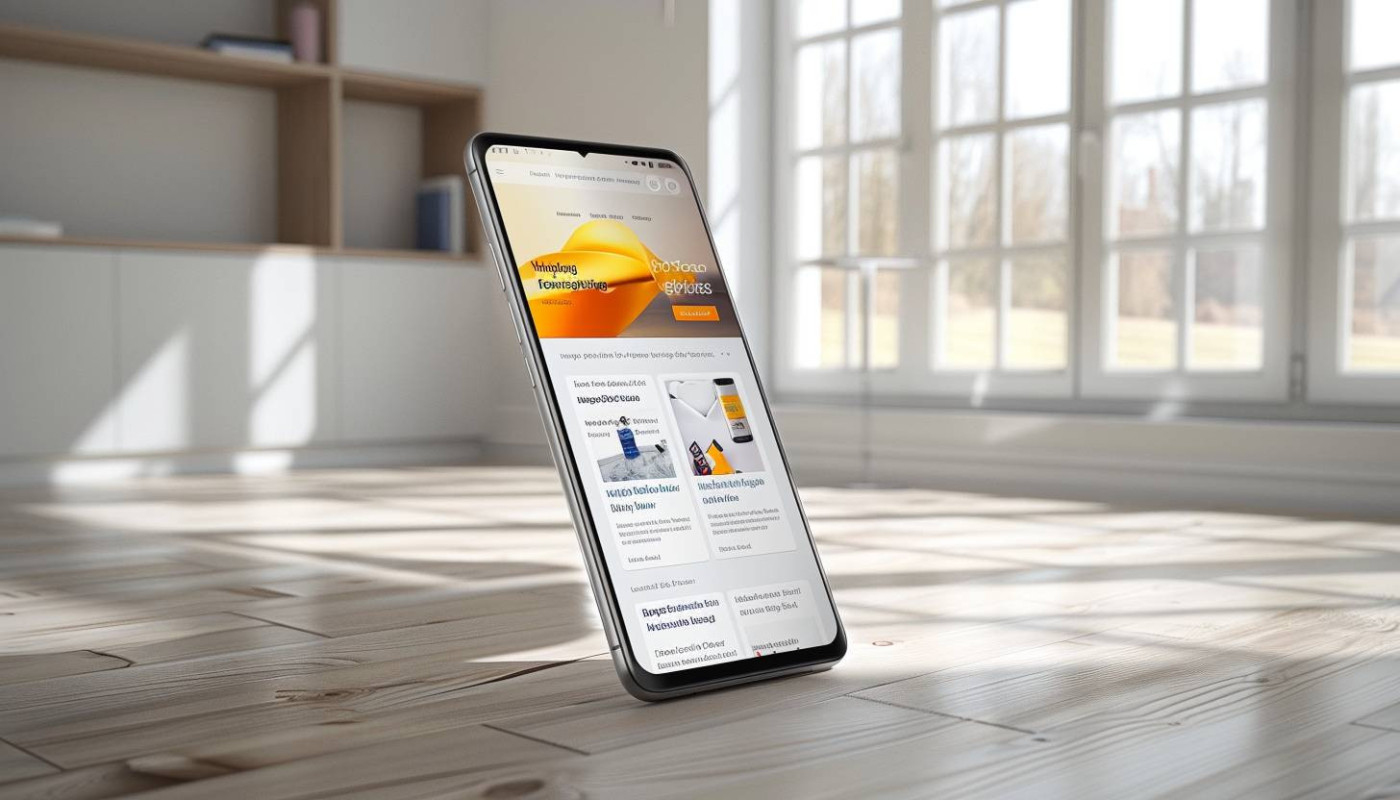
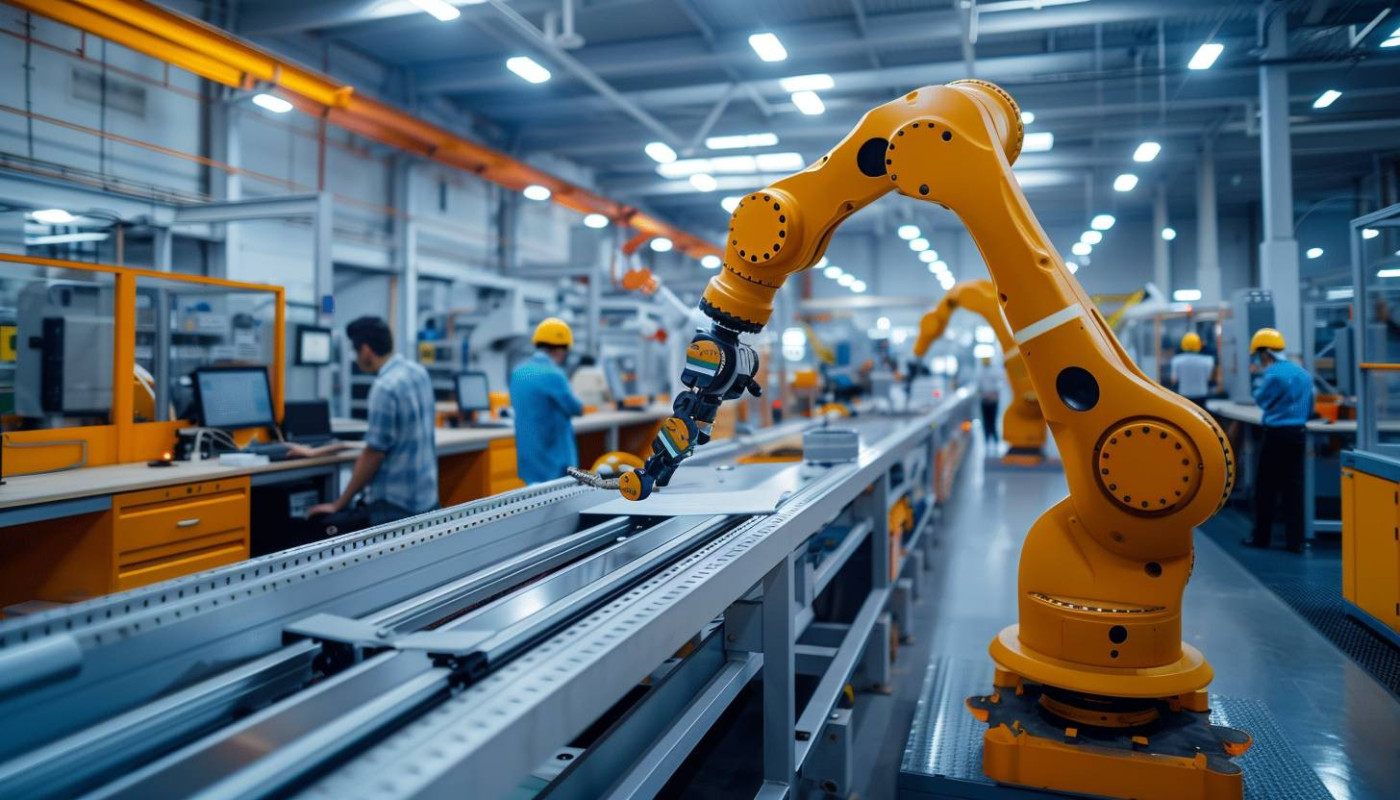
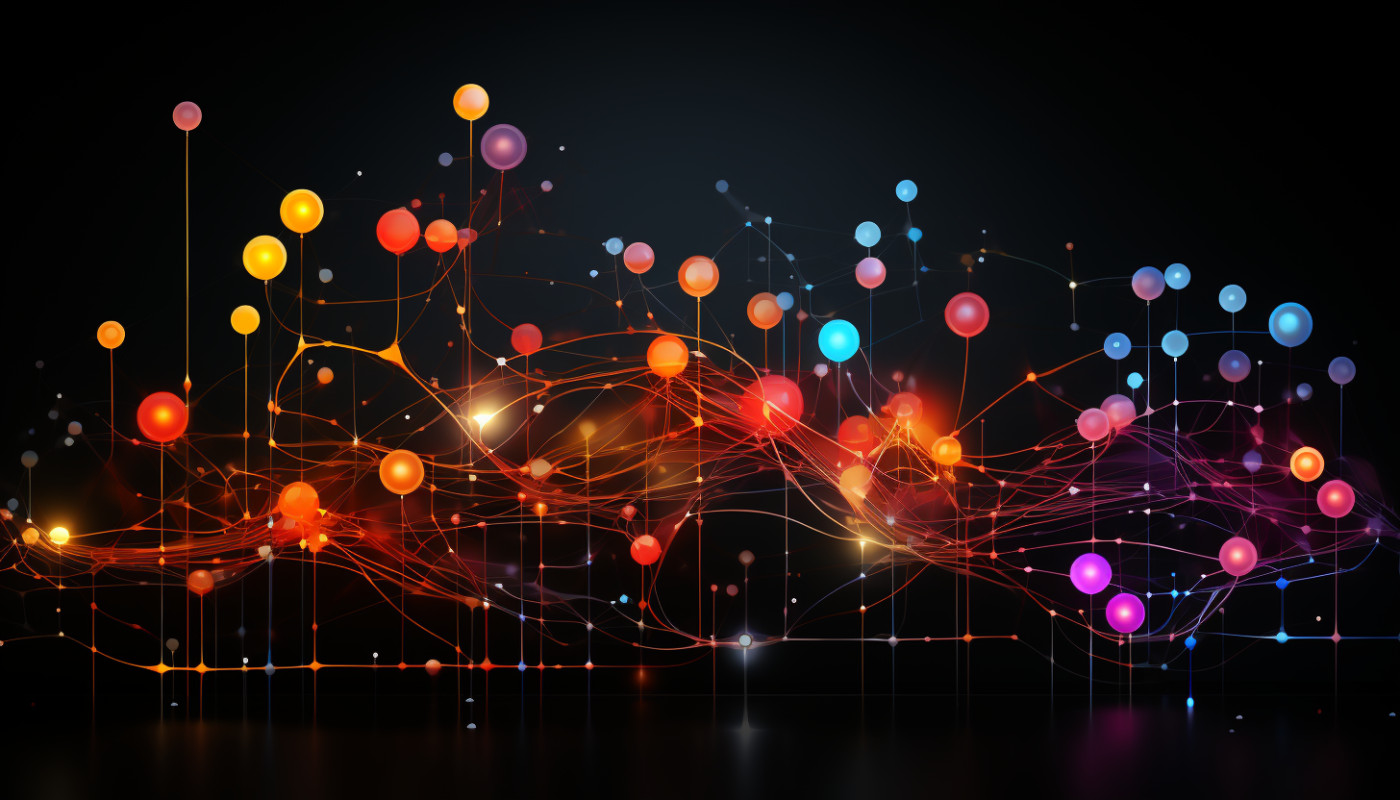
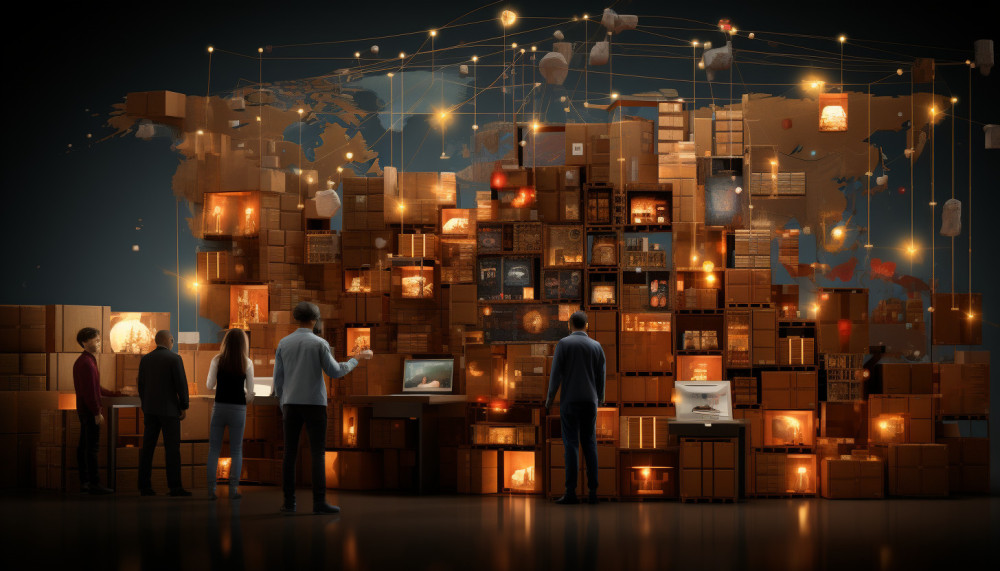